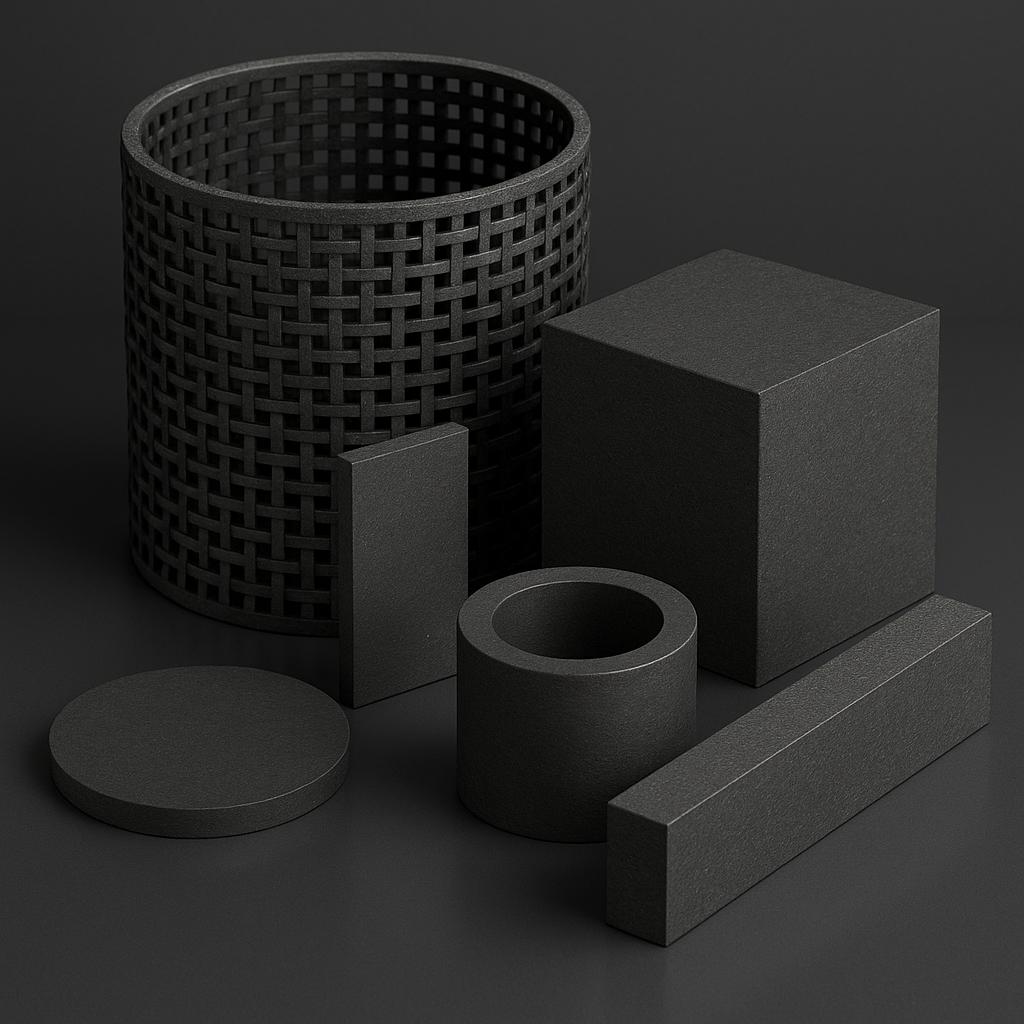
Современная вакуумная техника предъявляет всё более жёсткие требования к материалам, способным работать в условиях высоких температур и глубокого разрежения. Особое место в этой сфере занимают композиты на основе углерода — материалы, сочетающие устойчивость к экстремальным нагрузкам с высокой термостойкостью и химической инертностью. Разработка и внедрение таких решений — результат работы инженерных коллективов и специализированных производств, среди которых можно отметить компании, занимающиеся созданием высокотемпературных углеродных компонентов для вакуумной промышленности, таких как Карбосил, ознакомиться с услугами которой вы можете на https://karbosil.com/. В данной статье рассмотрим, какую роль играют углеродные композиты в высокотемпературном вакуумном оборудовании, за счёт чего они столь востребованы и в чём особенности их применения.
Почему углерод: уникальные свойства основы
Углерод — один из немногих материалов, способных сохранять стабильность структуры при температурах выше 2000 °C в инертной или вакуумной среде. При этом он обладает рядом дополнительных преимуществ:
- низкий коэффициент теплового расширения;
- высокая теплопроводность (в зависимости от структуры);
- отличная термостойкость;
- устойчивость к термоударам;
- химическая инертность в большинстве сред;
- способность работать в условиях глубокого вакуума без выделения газов.
Эти характеристики делают его идеальной основой для создания композитов, предназначенных для использования в высокотемпературных вакуумных системах.
Что такое углеродные композиты?
Углеродные композиты — это материалы, в которых углерод используется как основа, а дополнительные компоненты (чаще всего — армирующие волокна, наполнители, связующие) улучшают механические или термические свойства. В контексте вакуумного оборудования чаще всего используются:
- углерод-углеродные (C/C) композиты — состоящие полностью из углерода (матрица + армирующее волокно);
- углерод-графитовые композиции — сочетающие структуру прессованного графита и армирующие компоненты;
- углеродные материалы с керамическими упрочняющими фазами — для повышения износостойкости.
Особенность C/C-композитов заключается в том, что они сохраняют форму и свойства даже при многократных циклах нагрева и охлаждения. Это особенно важно в вакуумных печах, установках ионной имплантации, установках напыления и других промышленных агрегатах.
Основные области применения
Композиты на основе углерода нашли применение в различных сегментах вакуумной промышленности:
- Нагревательные элементы вакуумных печей
Углеродные ленты, стержни и каркасы нагревателей работают стабильно при температурах до 2500 °C. Их высокая теплопроводность способствует равномерному распределению температуры в камере. - Теплоизоляция и экранные системы
Многослойные тепловые экраны из углеродных материалов снижают теплопотери и минимизируют излучение тепла, сохраняя энергию и ускоряя рабочие циклы. - Оснастка для термообработки
Поддоны, подставки, направляющие и другие элементы, выполненные из C/C-композитов, обладают высокой механической прочностью и не деформируются при нагреве. - Элементы вакуумных камер и манипуляторов
Лёгкий вес и термостойкость делают композиты на основе углерода удобными для динамически нагруженных систем и перемещающих механизмов. - Катоды и мишени в ионных и плазменных установках
За счёт чистоты и стойкости к ионизации углеродные материалы устойчивы в агрессивной среде, не загрязняя поверхность изделий.
Производственные особенности
Изготовление композитов на основе углерода представляет собой сложный многоэтапный процесс, включающий:
- формование заготовок из углеродного волокна (ткани, нити, 3D-структуры);
- пропитку связующими веществами (пек, смолы);
- термообработку при высоких температурах;
- карбонизацию (превращение связующего в углерод);
- возможную графитизацию (дополнительное термическое уплотнение);
- финишную механическую обработку и контроль качества.
В зависимости от задачи, параметры этих этапов могут сильно различаться. Особое внимание уделяется минимизации остаточного газа в структуре материала, чтобы он не мешал достижению высокого вакуума.
Преимущества и ограничения
Преимущества:
- выдерживают температуры выше 2000 °C;
- не плавятся и не деформируются;
- устойчивы к воздействию большинства химических веществ в вакууме;
- не выделяют газов, если правильно отожжены;
- обладают длительным сроком службы при циклических нагрузках.
Ограничения:
- высокая стоимость производства;
- хрупкость при ударных нагрузках;
- окисляемость при контакте с воздухом при высоких температурах;
- необходимость хранения и эксплуатации в инертной среде или вакууме.
Перспективы развития
На фоне роста спроса на вакуумные технологии — в производстве электроники, материалов, энергетике и аэрокосмической отрасли — наблюдается активное развитие и улучшение углеродных композитов. Особенно перспективными считаются:
- наноструктурированные углеродные композиты, повышающие прочность и теплопроводность;
- гибридные материалы с элементами керамики или металлов;
- автоматизированные методы производства, снижающие себестоимость.
Большое внимание также уделяется экологической безопасности и переработке использованных материалов. Повторная термическая обработка позволяет восстановить часть эксплуатационных характеристик.
Заключение
Композиты на основе углерода стали ключевыми элементами в создании надёжного и эффективного вакуумного оборудования для высокотемпературных процессов. Их уникальные свойства позволяют обеспечить стабильную работу установок даже в самых жёстких условиях. При этом область применения таких материалов продолжает расширяться — как за счёт технологических усовершенствований, так и благодаря растущим требованиям к точности и чистоте вакуумных процессов.
Для тех, кто занимается проектированием и эксплуатацией вакуумной техники, важно понимать не только свойства самих материалов, но и принципы их правильного выбора и обработки. Именно это знание обеспечивает высокое качество и надёжность всей системы в целом.